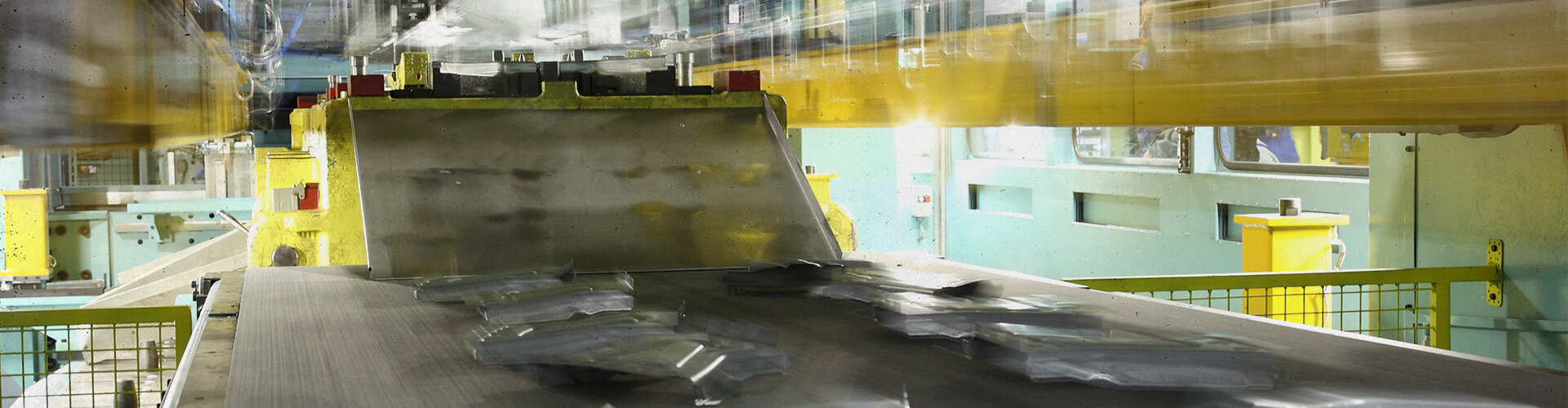
Transfer Automation
Transfer Automation - Flexibility and Productivity for the Press Shop
At DREHER Automation, we offer our customers transfer systems for small forming presses up to large capacity presses, even those with several press tables or for press lines. Our transfer system automation is the right solution for every press type and brand.
We supply transfer systems for e.g.:
- Eccentric presses
- Knuckle-joint presses
- Hydraulic presses
- Multi-column presses
- Highly dynamic servo presses
Make your manufacturing process more flexible, more productive, and safer with our transfer automation system.
Transfer Automation from DREHER Automation - Movement in new Dimensions
Our transfer system technology consists of modular construction kits in several sizes for all areas of application in forming technology. DREHER Automation stands for absolute flexibility in motion sequences, especially thanks to the use of separate drive technology.
Integrated Control Concept for your Transfer Press
DREHER Automation has developed a consistent control concept based on Siemens components for various handling tasks. An integrated automation solution is established featuring the Simotion D Motion Control System, inverters from the Sinamics S120 family, and servo motors from the 1FK series. This transfer automation system can be adapted exactly to the respective task in terms of performance and functionality.
With the help of our specially developed control system for transfer automation, the individual axis movements are optimally coordinated with one another and precisely adapted to the stroke movement of the transfer press. With this control concept, it is also possible at any time to set-up an interface to other line components such as coil processing lines, blank destackers or blank stackers, easily.
Flexibility for your Transfer Press
Separate drive technology ensures flexibility, and the software package developed by DREHER Automation implements it. In this context, it does not matter whether the task at hand is to integrate additional axes, program special sequences, or control cams. Be it position-controlled, angle-synchronized, time-controlled, or dynamic: DREHER Automation can always provide the right solution.
Maximum Productivity for your Transfer Press
You can count on DREHER Automation for expertise in linear movement. The highly dynamic servo drives, and the entire drive train are engineered and designed according to your specific requirements. This ensures optimum output and excellent availability over a long period of time.
Safety for Man and Machine
Personnel and machine safety is our top priority. As a result, DREHER Automation is making production plants safer with its “Adaptive Electronic Overload Protection” technology package. The software dynamically limits the available torque in the drive. This prevents the transfer automation system and the forming tool from being severely damaged by excessive force in the event of a fault.
Low Vibration Transfer Process
Today, vibration behavior can not only be positively influenced via mechanical factors such as the rail profile and material - electronic control systems also achieve clearly visible results. Therefore, DREHER Automation offers the “Active Vibration Compensation” technology package for its transfer automation systems. The resulting minimized vibration characteristics ensure maximum stroke rates with excellent operating smoothness. At the same time, the entire system is subjected to lower loads.
Energy-efficient Transfer Automation
In the field of energy management, DREHER Automation relies on the implementation of common intermediate circuits, for example with the forming press. This not only reduces the forming system’s overall energy requirements but also creates additional space for emergency strategies.
Spare Part Reduction
The modular system minimizes the need for spare parts, since the same motors, gears, or guides are used consistently in the drive trains, for example. In order to guarantee excellent availability of spare parts for your transfer automation system, DREHER Automation attaches great importance to using standard components that are available worldwide for both mechanical and electrical components.
Your Contact Partner
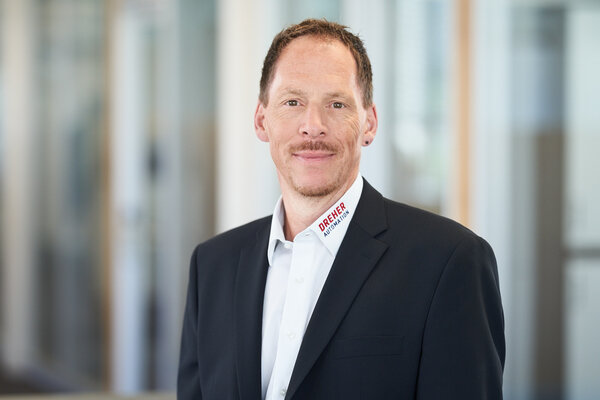
Marc-Andy Luippold
Senior Sales Manager
- +49 7454 881-501
- +49 7454 881-11
- m.luippold@dreher.de
Your direct Line to DREHER Automation
Do you have any questions or need some advice? Use our contact form, we’re happy to hear from you.
Product Portfolio
Transfer Automation
HotForge XL
Closing motion min. 0 mm - max. 300 mmLifting motion min. 0 mm - max. 300 mmFeeding motion min. 0 mm - max. 600 mmDimention transfer bar length 150 mm x height 150 mmTransfer Automation
HotForge M
Closing motion min. 0 mm - max. 150 mmLifting motion min. 0 mm - max. 200 mmFeeding motion min. 0 mm - max. 300 mmDimention transfer bar length 80 mm x height 80 mmTransfer Automation
HotForge L
Closing motion min. 0 mm - max. 200 mmLifting motion min. 0 mm - max. 200 mmFeeding motion min. 0 mm - max. 500 mmDimention transfer bar length 120 mm x height 120 mmTransfer Automation
FlexMotion S
Table length min. 2,500 mm - max. 3,600 mmFeeding motion min. 0 mm - max. 800 mmClosing motion min. 0 mm - max. 200 mmLifting motion min. -30 mm - max. 120 mmTransfer Automation
FlexMotion M
Table length min. 3,000 mm - max. 4,250 mmFeeding motion min. 0 mm - max. 1,000 mmClosing motion min. 0 mm - max. 200 mmLifting motion min. -30 mm - max. 170 mmTransfer Automation
FlexMotion L
Table length min. 4,000 mm - max. 5,250 mmFeeding motion min. 0 mm - max. 1,200 mmClosing motion min. 0 mm - max. 220 mmLifting motion min. -30 mm - max. 220 mmTransfer Automation
FlexMotion XL
Table length min. 5,000 mm - max. 6,500 mmFeeding motion min. 0 mm - max. 1,500 mmClosing motion min. 0 mm - max. 250 mmLifting motion min. -50 mm - max. 250 mmTransfer automation
ProMotion M
Table length min. 3,200 mm - max. 4,100 mmFeeding motion min. 0 mm - max. 1,000 mmClosing motion min. 0 mm - max. 200 mmLifting motion min. -30 mm - max. 350 mm